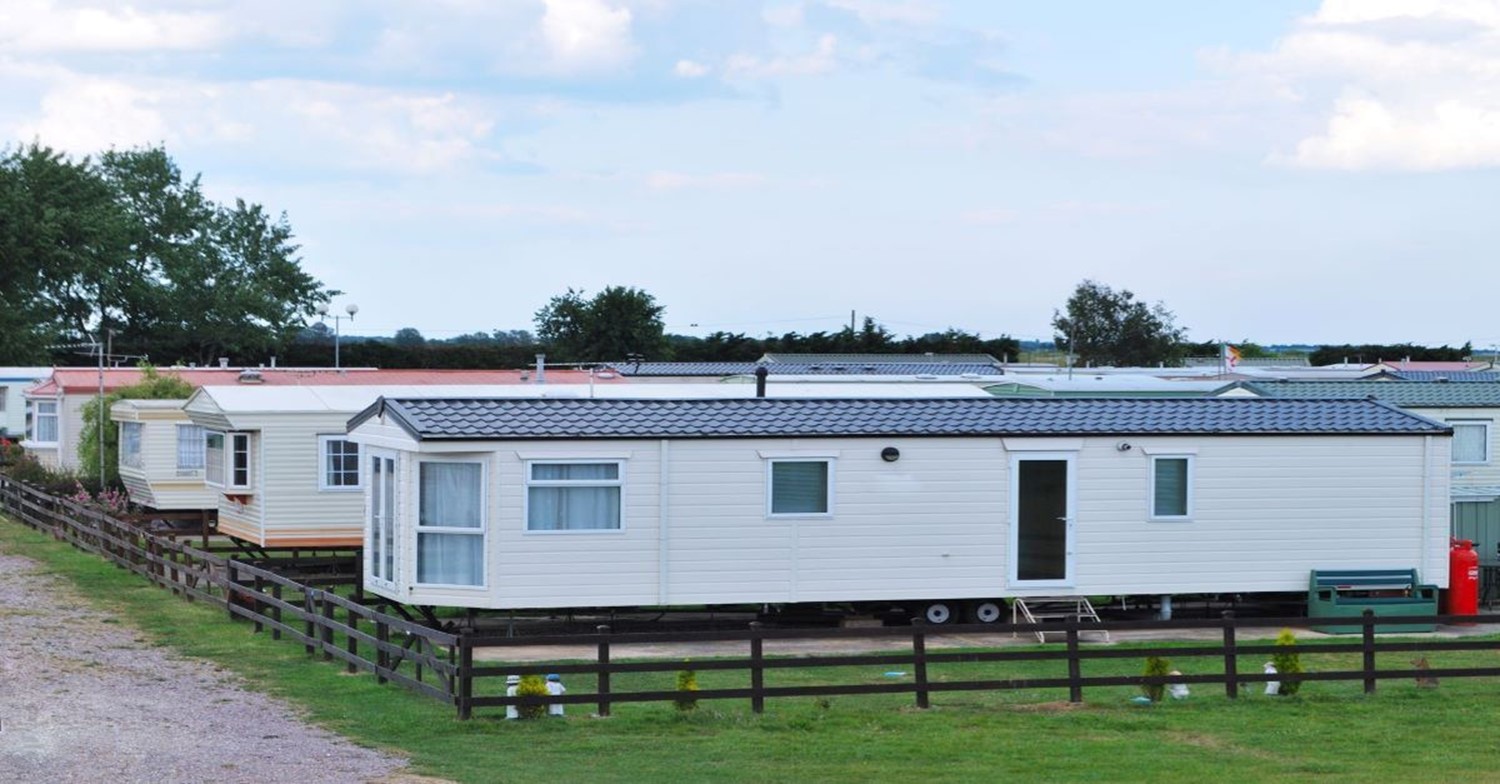
Look out below: A story from the front lines of manufactured home weatherization
In February 2020, Bob Pfeiffer and I trained a new implementation subcontractor for a manufactured housing pilot with a major Midwestern utility. Owner-occupants of manufactured homes seldom participate in energy-efficiency programs and therefore rarely reap the benefits they can provide. The pilot set out on a mission to change that by centering the experiences of manufactured home residents.
Our first manufactured home was owned by a retired woman whose elderly father lives with her on Chicago’s South Side. The crew began their duct inspections just like we taught them, working from inside the home first. They lifted the supply grilles and used a flashlight and mirror to inspect the truck line for leaks. Under the very first grille, just forward of the downflow furnace, they saw the dirt floor. A five-foot section of duct work was gone.
We reported this discovery to the homeowner, and she calmly said this must be why cold are comes up through the vents when the wind blows. She had been heating the underside of her home for who knows how long. Despite paying over $500 a month for utility bills, she and her elderly father never felt comfortable, saying that cold air blew through the vents even when the heat was on.
Bob did not hesitate to solve this problem the messy way. Dressed in full PPE, Bob and several other members of the crew crawled under the house to reconstruct that section of ductwork.
We found a solution on site to make sure the customer and her father would live comfortably, save money, and become more energy-efficient. The crew learned a valuable lesson about problem-solving and devised an approach to help more owner-occupants of manufactured housing.
The pilot ended in 2020 after serving 450 homes in the Chicagoland area. Even in our first live inspection and installation, we did not shy away from doing messy, demanding work to meet the needs of our clients. Our training, and the care and expertise we put into executing each repair, meant those 450 homes were safer, more energy-efficient, and more comfortable.
The work we did to help these families is the important work of weatherization. We can make positive improvements to their everyday lives by listening to their experiences and using our expertise to help remedy those problems.