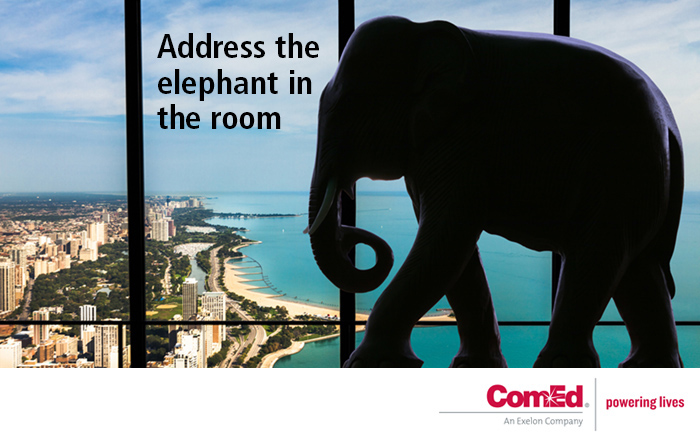
Window-to-wall ratio and Chicago’s path to deep efficiency
Building enclosure performance provides the largest remaining opportunity for deep energy savings in Chicago’s multi-family building sector. Vast areas of exterior glazing have a greater impact on energy consumption than any other decision in the design of residential high-rises.
In recent years, Chicago multi-family high-rises have been consistently built with large expanses of floor-to-ceiling glass yielding whole-building window-to-wall ratios (WWR) of 75 percent and higher. This far exceeds the prescriptive energy code threshold of 40 percent. The same multi-family building with 85 percent WWR will have 20–32 percent higher annual energy costs than a comparable building with 40 percent glazing. This high-rise trend should not be confused with the low-rise multi-family market, which already gravitates toward lower WWR, even for luxury residences.
Based on modeled whole-building performance; the savings from energy-efficient technologies such as LED lighting, smart thermostats, ENERGY STAR® appliances and high-performance heating and cooling systems can make a highly-glazed building minimally compliant with the Illinois Energy Conservation Code. These technologies are used to overcome the energy deficit from excessive glazing, rather than achieving deep efficiency and the goals of Architecture 2030. Amidst an urgent climate crisis, this is a huge missed opportunity.
The high-rise building sector in Chicago is experiencing significant activity with 44 new buildings under construction, compared to 17 this time last year. I am a member of the team who works with more than 70 percent of these properties through the ComEd Energy Efficiency Program new construction offering. I review designs and model energy use for new construction projects pursuing incentives. Since 2009, 450 new construction and major renovation projects have been served through the offering resulting in more than 215 million kWh in energy savings. Through the program, we hear the stories and understand the market momentum behind all-glass buildings. Lowering the WWR of multi-family high-rises offers an opportunity to save energy, improve occupant comfort, construct superior buildings and differentiate a developer’s multi-family portfolio. It’s time to get serious about this design challenge and evolve—and that doesn’t mean we have to sacrifice the wow-factor that has long distinguished Chicago architecture. It is the responsibility of the real estate community to demand innovation and the design community to inspire.
Deconstructing the sales pitch
High WWR is sometimes sold to clients as a way to provide more daylighting. But daylighting is more a function of strategic window positioning than of the quantity of glass. Daylighting modeling shows that a very high WWR can actually reduce the amount of useful daylighting to a space because it creates many hours of excessive, harsh light when occupants are likely to close blinds.
Floor-to-ceiling glass is also sold as providing greater views for tenants, but this is a misconception. When a person stands more than a few feet away, the window is a small piece of their overall view regardless of whether there is 100 or 40 percent glass in the exterior wall. It is only when the person approaches close to the window that they are immersed in the exterior view. Even then, there is little difference between the up-close view through floor-to-ceiling glass or through smaller windows.
Comfort and efficiency
Tenant comfort is compromised by high WWRs. Thermal analysis shows a strong correlation between glass area and thermal discomfort in winter and summer. In summer, there is excessive solar gain. In winter, there is radiant heat loss due to cold window surfaces and compounded by cold air drafts caused by convective air flow. A southwest-facing residential unit with floor-to-ceiling glass has approximately 1,000 more uncomfortable hours per year than a building with 40 percent WWR. About a third of the additional uncomfortable hours occur from 5 p.m. to 10 p.m. when units are typically occupied. Tenants need to move away from windows, close shades, change their clothing and/or adjust the temperature to compensate for the negative effects of the windows.
Mitigation strategies
Use of reduced solar heat gain coefficient (SHGC) glazing can be very effective in reducing heat gain from windows. This helps with cooling loads in summer; but can result, to some extent, in an energy and comfort penalty in winter when well-controlled solar gain could provide some passive heating in Chicago’s cold climate. It is important to strike the right balance for the specific window orientation and overall building performance goals.
Designers sometimes consider adding extensive exterior shading to overcome some of the visual and thermal comfort issues caused by large areas of glazing. Unfortunately, exterior shading is quite often eliminated due to high first cost. Even when exterior shading is included in the construction; final attachment details can result in poor overall building performance including higher energy use, potential material degradation and thermal comfort issues—all due to thermal bridging. Thermal bridging occurs where a thermally conductive material—e.g. concrete, structural framing members, aluminum window framing and other attachments or fasteners—penetrate the primary insulating layer of the building envelope. This provides a bypass route for heat loss or gain that significantly diminishes the net performance of the assembly.
Also, shading east- and west-facing windows to effectively reduce glare and heat gain is nearly impossible since sun angles shift so dramatically during the course of a day and throughout the year. At high occupancy times (mornings and evenings) in residential spaces, exterior shading on east or west exposures would do little to mitigate the need for interior blinds being drawn.
Designers also consider the use of more advanced window technologies such as triple-pane glazing systems with argon fill, low-emissivity (low-e) coatings, and even ‘smart glass’ technologies (e.g. electrochromic glass). While these technologies hold a lot of promise, in pure energy terms they are a long way from bridging the gap in performance between glazing systems and the thermal performance of code-compliant opaque-wall assemblies. The performance of triple-pane windows with argon and low-e coatings is still limited to about R-5.5 max (U-0.18) for the assembly including high-performance thermal barrier framing. Most often the glazing systems that get installed, due to first cost considerations, are the equivalent of an R 2.5. As a point of reference, in Chicago commercial buildings the wall assembly is required to have R-13 cavity insulation plus R-7.5 continuous insulation (U-0.064 assembly) in metal-framed construction—about triple the performance of the best window systems out there.
One powerful advantage of a lower WWR building is the flexibility to install radiant heating and cooling by reducing cooling loads in Chicago’s hot, humid climate. Radiant systems pump warm or cool water through the slab or panels in the space, controlling both air and surface temperatures. The energy required to pump water is less than what is required to operate fans in other HVAC systems and equipment runs more efficiently at the modest temperatures required for radiant systems. Next-generation radiant systems provide a quantum leap in performance and achieve deep efficiency. They also enable a clean interior design, superior comfort, better air quality and quiet operation.
Costs
A building with floor-to-ceiling glass and standard glazing costs $0.14-0.36 per square foot more per year to operate than a building with 40 percent WWR. For a typical two-bedroom condo, the added cost amounts to $4,000-10,800 over the life of a 30-year mortgage. Even without considering the current low cost of energy, there is generally little motivation for developers to consider the energy costs incurred by future tenants. Exceptions include buildings designed to achieve energy-related certifications that have been shown to increase initial sale value—LEED certification is the top one in this market. New trends in city energy policy, energy benchmarking disclosure, energy efficiency incentives and innovative financing have brought annual energy costs into the conversation with multi-family developers. Energy benchmarking may become a significant market factor as energy performance data becomes widely available online for nearly every large building in Chicago.
Standard glazing in window-wall and curtain-wall systems is often the same cost or cheaper than well-insulated opaque wall assemblies designed to work with those same framing systems. In high-rise applications; opaque assemblies must be robust enough to withstand wind loads contributing to their higher cost. Labor costs are higher for opaque assemblies that must be built up compared to modular systems that can be installed quickly. Lastly, volume pricing for high amounts of glass on a façade results in lower per unit costs.
Premium efficiency glazing and exterior shading come with a prohibitive first cost premium. It follows that developer-led projects typically gravitate toward the lowest first cost option of a high WWR with market-standard glazing. For a lower WWR building to be competitive, opaque assemblies must be specifically designed for lower material and installation cost. Lower WWR building project engineers must capture the cost savings from reduced HVAC system size, reduced or eliminated perimeter heating; and potentially, eliminated ducted, forced-air heating and cooling.
Successful designs do not happen by accident. They happen when the owner, architect, engineers, cost estimator, general contractor and subcontractors are all at the same table early in the design process. This is how integrative design results in a superior product.
Learn more
If you want to learn about strategies for designing lower WWR multi-family high-rises and alternatives to floor-to-ceiling glass watch this webinar and read this technical paper. Both of these initiatives expand upon this topic and broaden the discussion to other high-performance envelope considerations.